Your warehouse is full of inventory, but how do you get an accurate picture of what is on any given shelf tomorrow? Next week? Later this afternoon? You could get your warehouse staff to conduct a physical inventory, auditing your entire facility’s stock. But unless you are running a small operation with limited SKUs, a physical inventory can be a massive disruption. It may necessitate closing your shipping and receiving operations for an all-hands-on-deck count, inconveniencing your customers and causing serious delays. That’s where cycle counting comes in.
HOW CYCLE COUNTING WORKS
Cycle counting is an invaluable inventory auditing method to identify and rectify discrepancies in stock records. Where a physical inventory is labor and time intensive as you count all the stock in the building, cycle counting is the process of auditing a smaller, pre-selected portion of your inventory at set times throughout the year.
An inaccurate inventory count is one of the leading ways companies lose money and miss out on sales. Miscounts on your warehouse floor can quickly affect your ability to fulfill orders and lead to excess costs on inventory you did not need to store and products that are not selling. The effects on inaccurate inventory counts can impact not only your warehouse management but also your sales forecasting and logistics planning for years to come.
With cycle counting, you break the massive task of performing a facility wide physical count into manageable segments. While a portion of time is allocated to conducting a count in a section of your warehouse or on a particular product, the rest of your facility continues operating as per normal. Once the count has been completed you move on to the next section or product in your warehouse, continuing until you cycle back to where you started, ready to audit those numbers again.
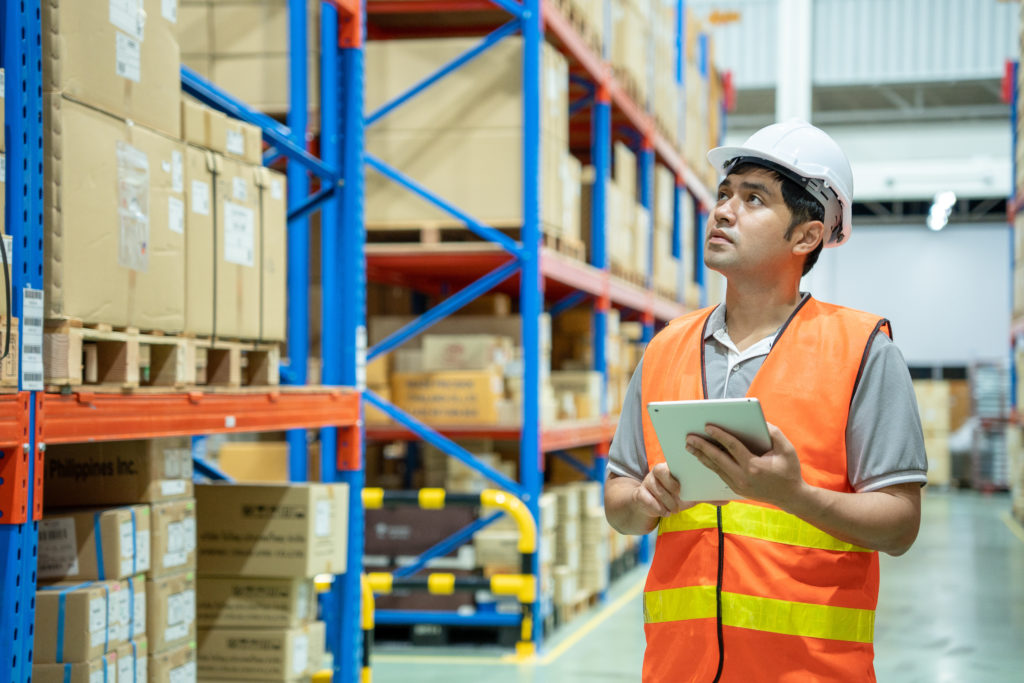
IMPLEMENTING A CYCLE COUNT
Build a schedule for which products or sections of your warehouse you are cycle counting. Prioritize what stock items are the most profitable or moving the fastest off your shelves. If your company carries any seasonal items, you should time your cycle count of those products to occur during their peak demand. Using a warehouse management system (WMS), you can quickly pull this data to determine which inventory to prioritize when.
Determine the time you want the cycle count to occur. Some companies prefer the duty to be performed at the beginning of an employee’s shift, when they are fresh and sharp, while others like to take advantage of the drop in productivity towards the end of an employee’s shift by assigning them the less labor-intensive duty of performing a count.
Using a WMS, upload a cycle count report to the employees assigned to the count. Remember to make sure that you have closed all transactions for the inventory being counted before the employees begin auditing.
When performing a cycle count, your team should review the inventory quantities, descriptions, and locations listed in the report uploaded to their mobile units. Any discrepancies between their findings and the report need to be investigated and taken to their manager. Patterns of error need to be closely documented so the right solutions can be found to rectify the issue.
Once the count is complete, update the inventory report with the actual stock on hand and schedule the next time to review this portion of your warehouse’s inventory. The frequency with which you will repeat a cycle count will depend both on the level of inventory you carry and the number of employees you have available to perform counts, however in an ideal world it is best practice to review each product line quarterly.
As you begin to perform recurring cycle counts, look for patterns of inventory errors. Use the data your team has collected to try and figure out what is causing a mismatch between the reported numbers and actual to try and find solutions to mitigate the problem. If employee theft becomes a concern, assign employees who do not normally work in that section of the warehouse to perform the count and randomize your cycle counts to keep employees off guard.
TYPES OF CYCLE COUNTING
Different inventory situations call for different means of auditing your stock. Lets look at several at your disposal.
ABC Cycle Count
As we discussed in our last post, ABC cycle counting is the process of ranking your inventory by your “A” products or most valuable, “B” products and finally “C” (read how to determine which of your inventory is which here).
Once you have categorized your inventory, you can build a cycle count schedule which prioritizes more frequent counting of the ‘A’ group of inventory and less of the ‘C’ inventory. This allows your facility to minimize counting while ensuring an accurate count of your highest valued assets. For example, a company may opt to count all of the ‘A’ inventory weekly, the ‘B’ inventory quarterly, and the ‘C’ inventory every six months.
Usage (or Frequency) Cycle Count
Usage-based cycle counting, also known as frequency-based cycle counting, is built around the idea that the items that are most often touched are the ones most likely to incur errors in a count.
Say you had a bin of razor blades in your inventory. If that bin is picked only once a day by one person the chances of a miscount are one. But if you have twenty employees a day picking razor blades from that bin, there are now twenty chances an error may occur.
To set up a usage-based cycle count, divide your warehouse into zones and log the frequency employees interact with each zone over a 90-day period. With a proper warehouse management system in place, you can quickly collect the data and assign a usage ranking to each zone. From there you schedule counts based on the areas with the most touches.
Control Group Cycle Count
For this method, you will want to pick a small selection of items in your warehouse. You then count them frequently over a small period of time, say at the end of every shift for a week. As you begin to collect data, the repetitive nature of the count should expose any errors in your day-to-day tracking of inventory.
The idea behind a control group count is to figure out how and why errors occur, and to apply the solution to the problem across your entire facility.
Opportunistic Cycle Count
Where the previous cycle counts we have discussed are scheduled, an opportunity-based count occurs during critical stages in inventory management. You can instruct employees to conduct a count when an order is placed or when stocking inventory. You can also use your warehouse management software to set thresholds such as when a stock goes below a certain number your employees are instructed to perform a count. Another standard time to perform an opportunistic cycle count is when your warehouse is shipping less product than the customer ordered, known as short-picks.
Random Sampling Cycle Count
As the name suggests, this is a method wherein you select stock items at random to count. This method is performed in one of two ways. The first is known as constant population counting, wherein the items you count are truly random so there may be several times in a row where you count the same product. To avoid overlooking any inventory for an extended period of time, some warehouses opt for a diminishing population count. This method excludes any inventory that has already been selected for a random count until every item in your facility has been audited during a cycle count.
Surface Area Cycle Count
Finally, you may opt to perform counts based on sections of your facility as opposed to specific inventory. For this method, you need to divide your warehouse into zones. An auditor will then perform a cycle count on all the inventory in their assigned zone, regardless if it is identical or varied.
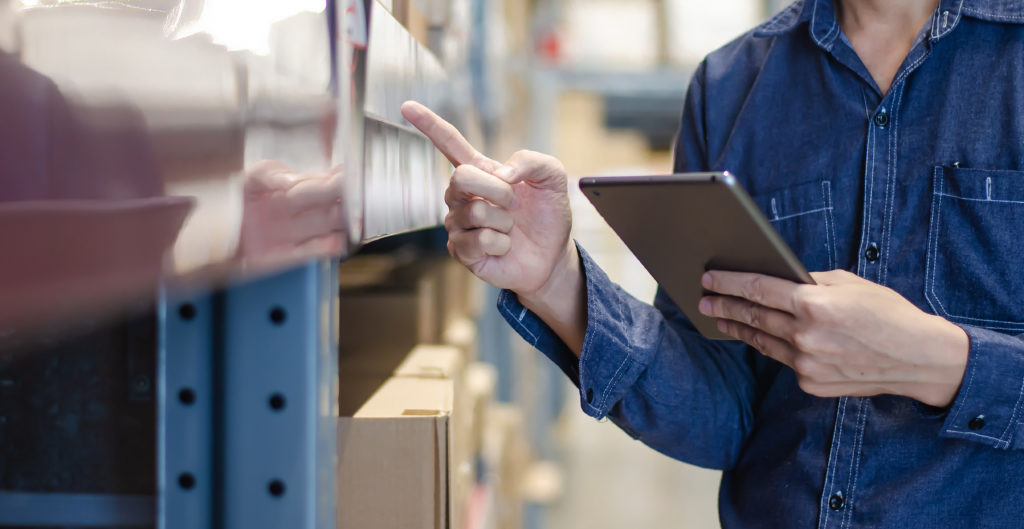
CYCLE COUNT WITH A WMS
One thing that you may have noticed has come up throughout this topic is warehouse management software. Performing a pen and paper count of your inventory is odious and prone to human error which is why a WMS is essential to conducting a proper cycle count.
Using barcode and RF technology, employees can quickly scan items into their inventory report. They can see on their mobile devices the results of previous counts and compare their numbers to what the expected inventory on hand was, seeing in an instant any errors. Real time tools found in warehouse solutions like our K.Motion Edge introduce system driven cycle-counting and empty bin checks to ensure that stock accuracy is maintained and discrepancies are flagged immediately.
A WMS can also remind your employees to conduct a cycle count and can direct them to the items or locations where a count should be performed on any given day.
THE BENEFITS OF CYCLE COUNTING
Knowing the difference between what you physically have on hand and what your inventory management software thinks you have on hand is essential to any warehouse facility being able to run properly and profitably.
On any given day a human error such as improperly scanning an item or theft could distort the numbers from what your reports think you have. Over time errors will build up and costs to your company’s bottom line will intensify. You will start finding your facility unable to fulfill orders you thought you were stocked for while products you did not know you were still housing will take up unnecessary storage space and lead to overstocking.
A study from the Harvard Business Review found that companies lose half of intended purchases due to stock-out. The report goes on to say that for a billion dollar company, this loss in purchases yearly comes out to $40 million. But it does not have to be that way.
With cycle counting you can get a snapshot of your inventory on hand without grinding to a halt for a costly and time-consuming facility wide physical inventory count. With an accurate inventory count, you will keep your customers happy while reducing both overhead and margins.
Cycle counting is one of the simplest yet most effective tools at your disposal to running a profitable warehouse and with Körber’s line of warehouse management software it is a methodology we can seamlessly integrate into your operations today.
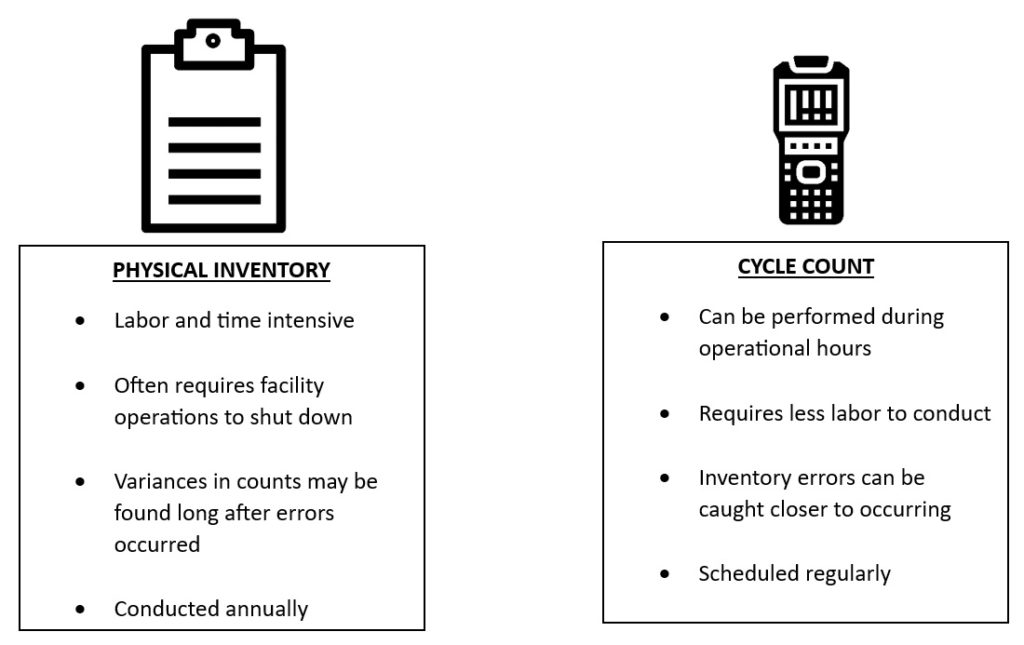