In an earlier blog we discussed ABC profiles and cube movement distribution. Through this analysis you should be able to determine if products are frequently ordered together. If you do see a significant correlation between products, consider storing the products together to help reduce overall travel time per pick tour. If the pick correlation frequency is consistently high, you may even think of these as informal kits. For example, when diapers are ordered, clean wipes are also ordered 70% of the time. This is a high percentage and can significantly increase pick labor productivity. This is also a simple approach to managing ‘kits’ without the additional space and duplicate inventory requirements for the kits and the individual component items.
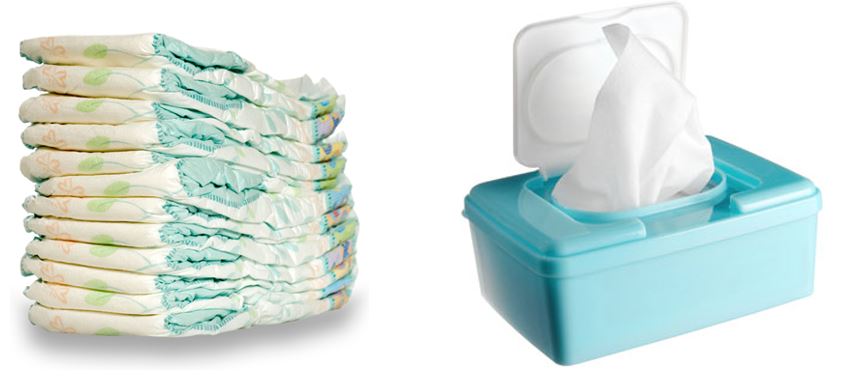
Alternatively, you should be cautious when storing like product together. In an automated warehouse you might be confirming the pick by a bin address and/or product bar code scan or voice input. This is a built-in quality assurance check that helps improve overall pick accuracy. However, unless you are working in a robotics warehouse, people will still be the main form of order processing. And people can and do make simple errors, even then they have the best intentions. Even in a scan-based pick flow, it is possible to scan the right product but pick the wrong product. This happens when the operator scans a location, turns away from the location to chat with another employee or pick up something they dropped, the turn back to the wrong location and pick the wrong product. Certainly not highly probable, but possible.
One way to reduce this mis-pick potential is keep visually similar products separate in the warehouse. Or at least not stored side by side. Storing similar products next to each other could cause miss-picks if operators do a visual pick by product. This could be challenging when pickers are tired and/or rushed. For example, the untrained eye may find it difficult to tell the difference between a two way and three-way light switch.
Another concept to consider when designing pick slots is to try to minimize the amount of congestion in aisles. For example if you setup a pick zone slotted with mainly high volume A items, the aisles may become crowded if multiple pickers are sent to the same aisle or bin to complete picks. A way to avoid this is spread out pick slots based on ABC calculations and/or setup multiple pick slots for the same product throughout the pick zone. Using technology to identify item level ABC criteria, and determine or suggest pick slots will help in your efforts to minimize some of these potential pick issues discussed. Alternatively you can work with a third party to perform the detailed analysis required to help you get a better understanding of your orders and operations to support your continuous improvement efforts.