A basic principle to optimizing warehouse space is evaluating and selecting the most space efficient storage equipment. Using more dense storage equipment is a key factor to reduce space requirements. An analysis of your products inventory levels and cubic order activity should be performed to accurately define the storage requirements in reserve and the forward picking area. With the requirements clearly defined, the right decisions can be made on selecting from the various single-deep to deep-storage equipment options.
In most warehouses, there should be at least two to three different storage types used in the reserve and forward picking areas. If your warehouse has all single-deep pallet rack, then chances are you can utilize your space more effectively with the addition of different storage equipment.
If you do nothing else coming out of this session, I encourage you to understand your order profiles by analyzing 6 to 12 months’ worth of order history and develop a lines per order distribution graph similar to this Figure 1 and Table 1.
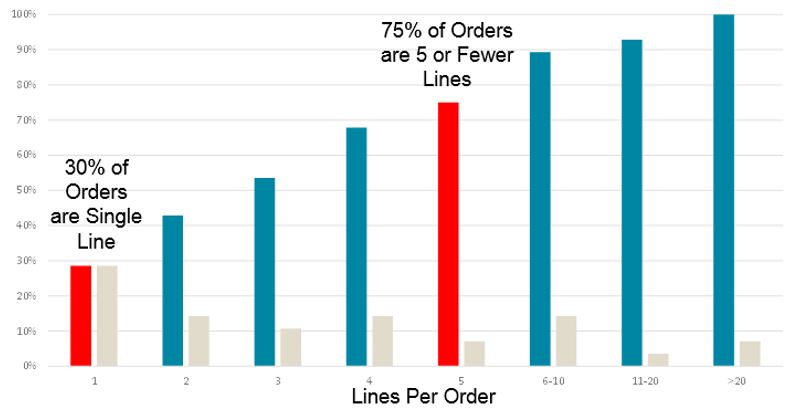
In the omni-channel supply chain, a typical wholesale distributor warehouse will have at least two to three different order types or profiles.
The table below is an example from a customer who sells through their own web store, to miscellaneous distributors and through large big box retail centers. We see 15% of their orders are medium sized, multi-line (from 2-10 lines), 35% of their orders are for big box replenishment and 50% are typical e-commerce single line single unit orders.
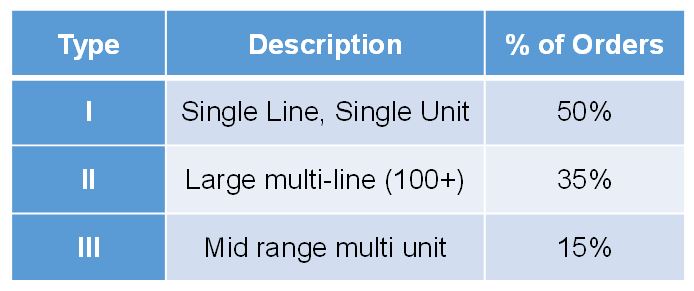
Knowing this information will help you define optimal pick workflows.
Once you know your order profiles, you can next perform a cube movement distribution analysis to help assess appropriate storage modes and space requirements. The most revealing analysis for determining storage mode and space albin decisions is the cube movement distribution.
Cube Movement
Cube movement is calculated by multiplying the number of times an item is picked, over a specific time period, times the storage cube of one item (or case). To make the use of cube movement distribution more efficient, it helps to group item cubes into specified ranges.
Figure 2 is an analysis cube movement distribution for a range of orders. In the example, 15 percent of the items ship less than one-tenth of a cubic foot per month. These items may be good candidates for storage drawers or bin shelving. At the other extreme, we see 12 percent of the items move more than 1,000 cubic feet per month, or nearly 20 pallets. These items may be candidates for block stacking, double deep rack, push-back rack and/or pallet flow lanes.
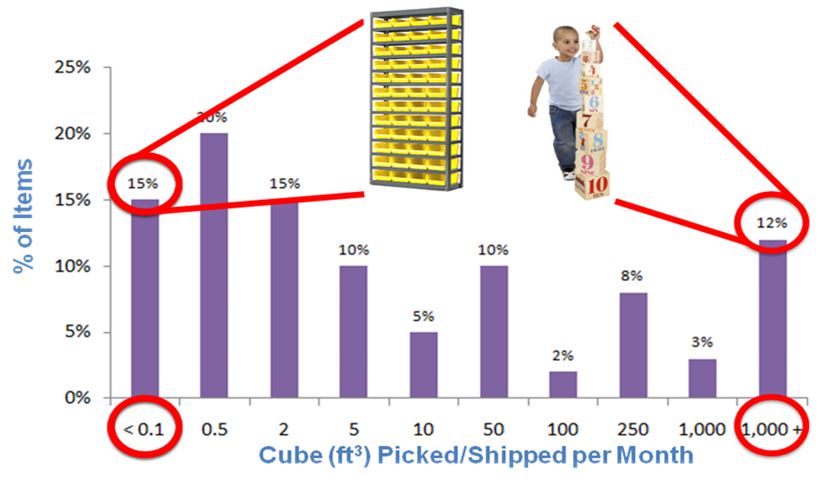
one properly, cube movement distribution slotting takes into account both cube movement and item popularity. Combined, these distributions can be used to define the types of storage medium to use to balance labor productivity, through-put and space utilization.
For example, items exceeding a certain cube-movement threshold are assigned to carton-flow rack (Figure 3). Items with high cube-movement popularity often need to be re-stocked frequently, and require a larger storage bin as compared to items with medium and low cube-movement which might be assigned to drawers, bin shelving or carousels.
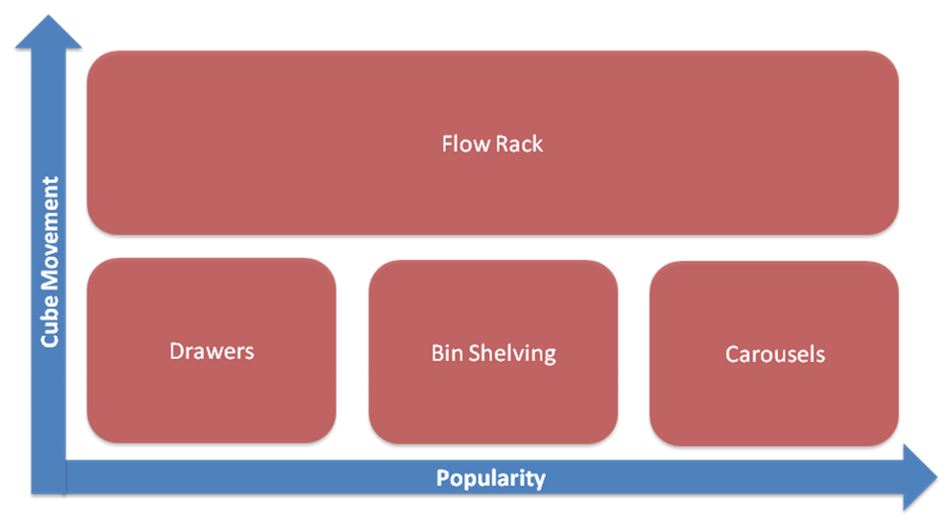
Placing slow-moving, low-cube items in bin shelving and fast-moving items in carton/pallet flow — or other appropriate storage options — improves storage density and picker productivity.