Do you have too much warehouse space? Chances are you are either out of space or getting close to it. It happens all the time, inventory (and other stuff) tends to expand to fill the amount of available space. When you do run out of warehouse space there are many options to consider including expanding your warehouse, building a new facility, or leasing outside space. Alternatively there are many proven, low cost concepts you should consider to improve the utilization of your existing space. In the first of a two part series, The Supply Chain Doctor Chris Barnes will be discussing various Space Utilization concepts.
Random vs. Dedicated Bins
There are two primary material storage philosophies fixed or dedicated bins and random or floating bins. In dedicated bin storage, each individual stock keeping unit (SKU) or item is assigned a specific storage bin. A given SKU will always be stored in a specific bin and no other SKU may be stored in the bin, even though the bin may be empty. Dedicated bin storage is analogous to a classroom where each student is assigned a specific seat.
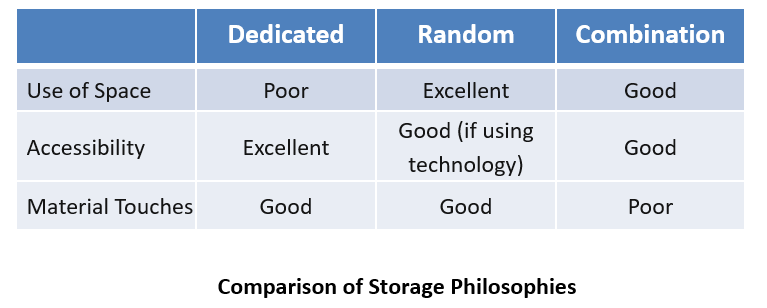
Choosing one storage philosophy over another means making a number of trade-offs between space, accessibility, and material handling efficiency.
Varied Bin Sizing
An often-overlooked method of reducing space requirements is optimizing the product bin sizes. Your warehouse may store and process a wide variety of product types and sizes. To effectively accommodate this variety, it is desirable to provide a variety of storage types and sizes. Trying to utilize only one type of storage media and bin size with a variety of products can lead to inefficiencies and low overall cube utilization. For example, as seen in the figure below, storing pallets with a consistent 44” pallet height into a 60” pallet storage opening is just wasting space. The right balance between tailored product bin sizes and flexibility results in improved space utilization.
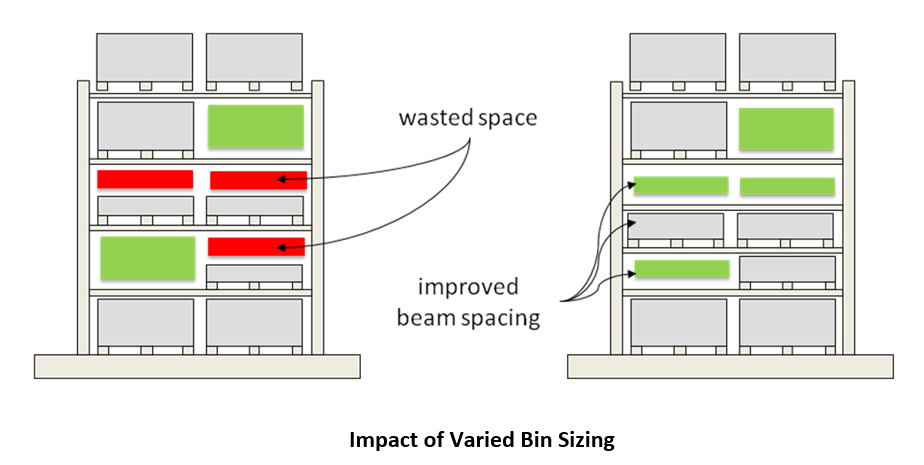
Storage Density, Velocity and Accessibility
Reducing aisle widths is a good way to improve space utilization. Thought should be made to the number of aisles used in your facility. The number of cross aisles and people aisles should be assessed to maximize the utilization of the aisles. The following table compares various storage utilization improvement concepts against expected velocity and capacity constraints.
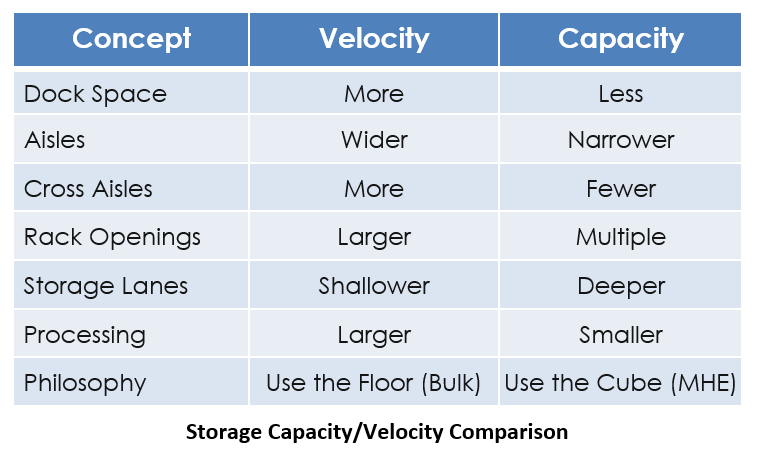