There has never been a more demanding or challenging time to run a warehouse. Staying competitive means navigating supply chain issues, the demand of a booming online sales market, and expectations of speedy delivery. Each operation has unique quirks, however, there are a few costly warehousing mistakes that every facility risks falling prey to. Avoiding them could have a major impact on your company’s bottom line…
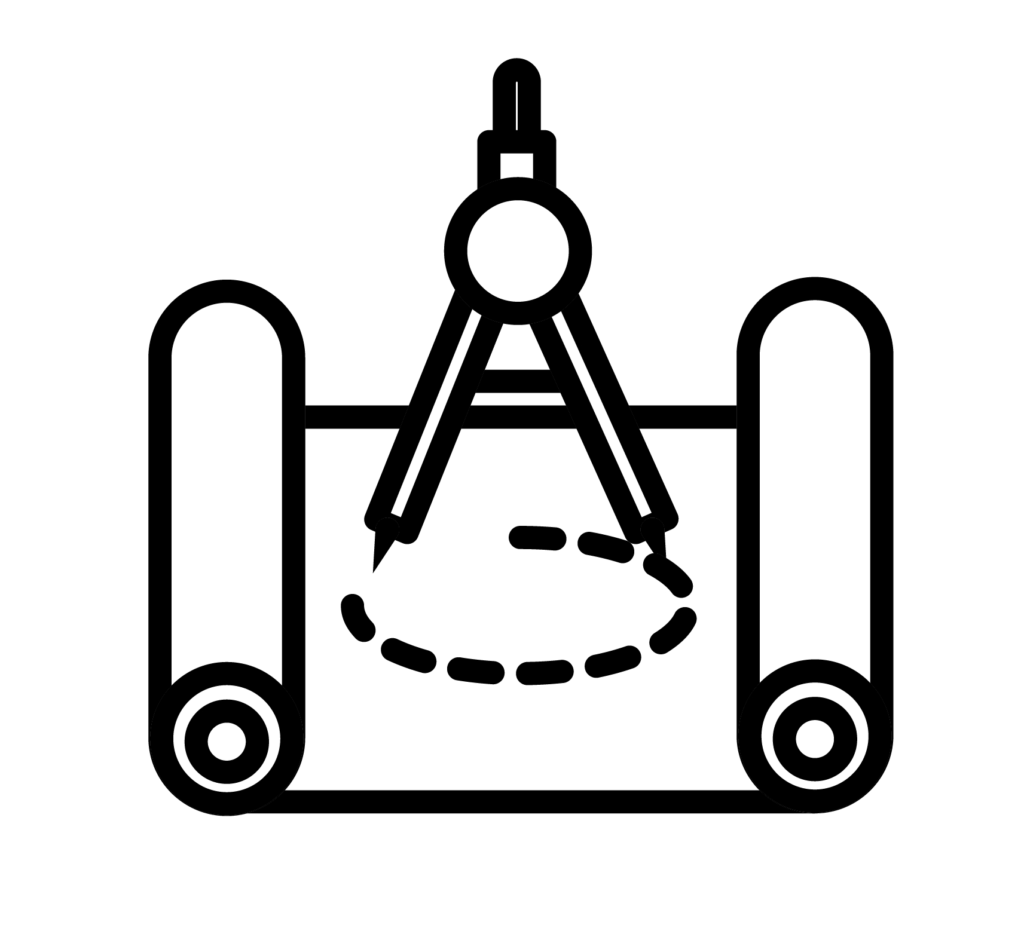
WAREHOUSE LAYOUT ISSUES
It all starts from the ground up. How you have designed your warehouse is the blueprint to how your employees will go about their day-to-day operations. We all want to maximize storage space, but creating aisles and work areas that are too small and which may restrict equipment is a recipe for slowing down operations.
While it can be tough to course correct once racks, shelving, and equipment have been installed, there are efficiencies you should look at with your current warehouse layout.
- Overlapping shipping and receiving areas: failing to have a clearly defined dock for both shipping and receiving is a common cause of costly errors and delays. A shared area creates bottleneck with inbound and outbound trucks, mixed up orders risk being reshelved, and delays at computer terminals are common as your employees work to track both items coming in and out of your warehouse.
- Not utilizing signage: providing directional cues to your employees, delineating the work that is carried out in areas of the warehouse, and marking paths for forklifts and other mobile equipment is the difference between keeping traffic on your warehouse floor moving or at a stand-still.
- Failing to maintain an organized workspace: cluttered, messy aisles and racks can add hours to a simple pick and pack. Staying on top of the cleanliness of your facility is paramount.
- No designated space for returns and overstock: in spite of best-laid plans, returns and overstock happen. Not carving out an area to handle them will put a strain on your whole facility. Establish housecleaning procedures after every shift so that the next shift can hit the ground running.
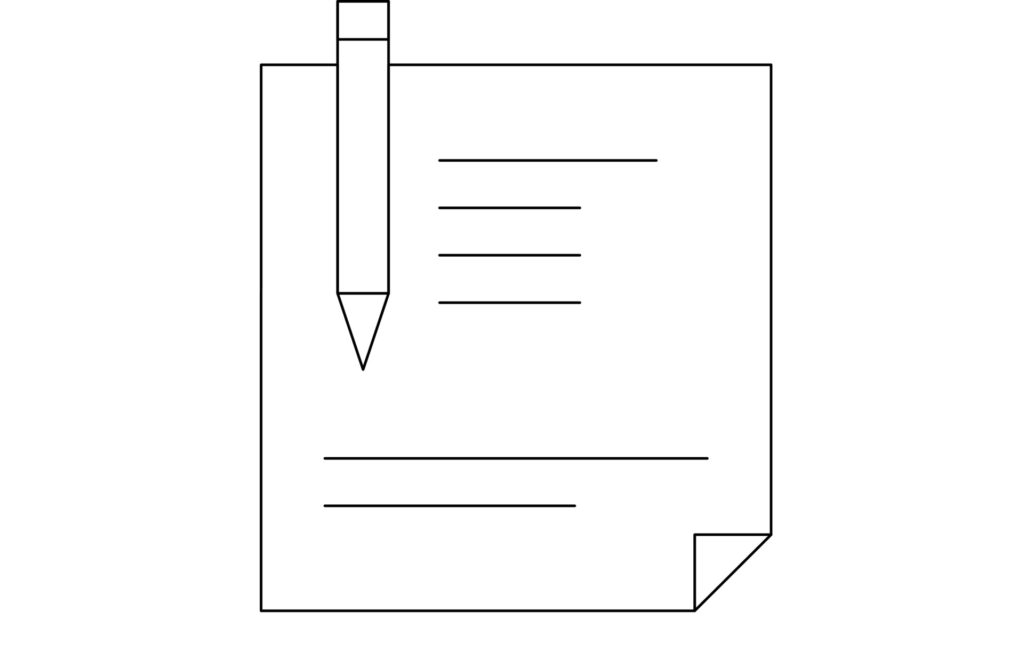
RELYING ON PEN AND PAPER
A pen might be mightier than a sword, but when it comes to your facility, it pales in comparison to a good warehouse management system (WMS). These systems have become widespread within the industry and not adopting them to your company’s workflow risks making one of the biggest warehousing mistakes that could leave your operation in the dust.
In 2022, inventory distortion worldwide was been measured at a whopping $1.9 trillion. This was caused by often avoidable issues like shrinkage, stockouts, and overstock. Yet one report found that 43% of American small businesses either don’t track inventory at all or are still relying on a manual system.
Manual data entry and excessive paperwork not only slows your employees down, it also creates room for costly errors where information can fall through the cracks. With a WMS, picking, packing, and shipping can all be automated through a barcode scanner system ensuring the proper product is where it needs to be.
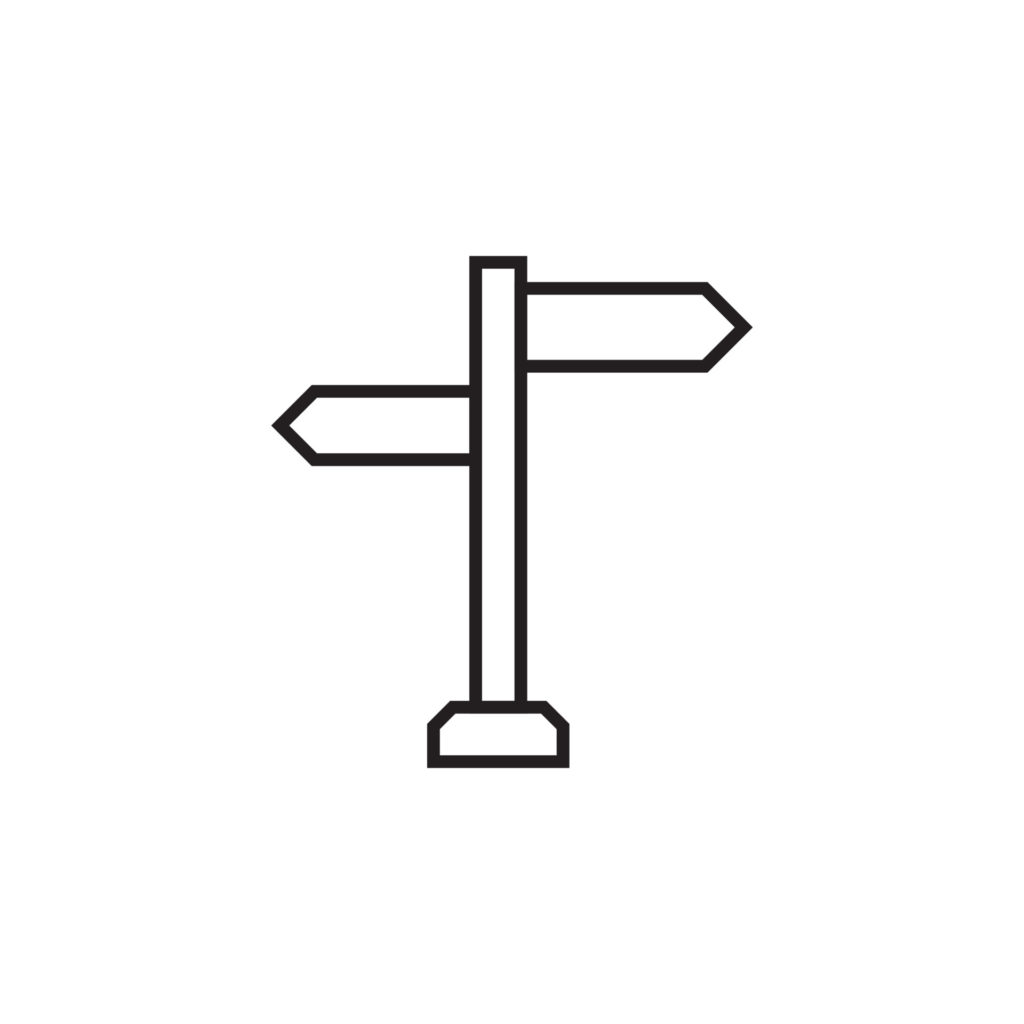
FAILURE TO OPTIMIZE PICKING PATHS
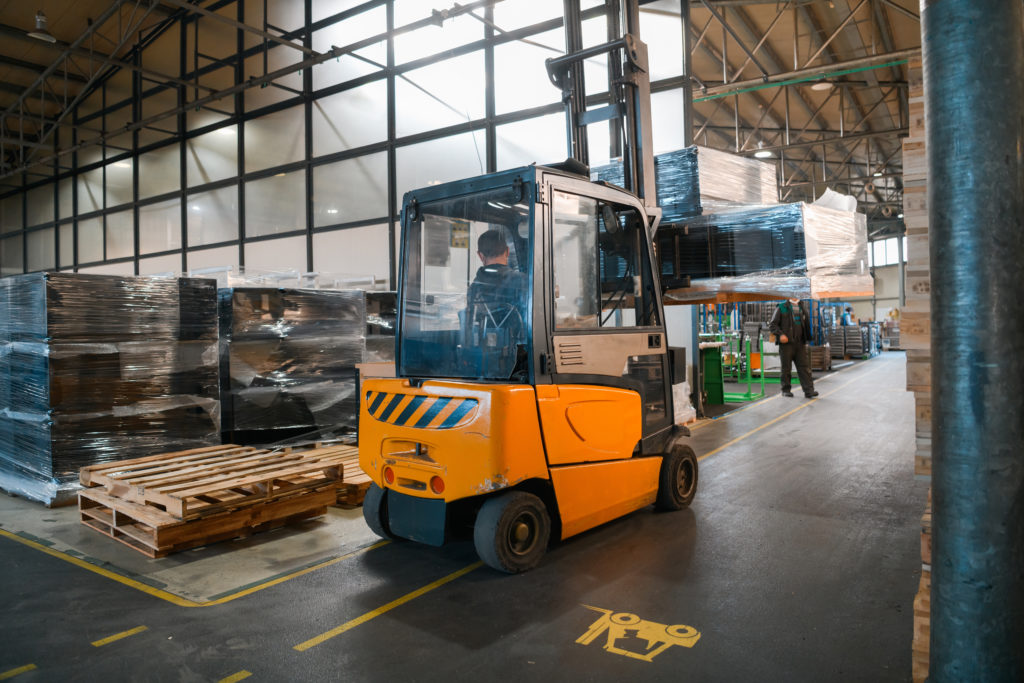
Successful warehouses require spending on the cost of labor needed to pick, pack, and ship orders in a timely manner. But that equation doesn’t just come down to the number of employees thrown at a job. It ultimately comes down to how efficiently they are able to do the task at hand.
Analyzing the location of items in relation to their pick speed will give you a snapshot of where time and energy is being misplaced. Warehouse management software can help you see items that are often picked together. This data allows you to rearrange your stock to keep these products on shelves near one another.
Travel paths and inventory flow data can help you identify bottlenecks both in the human movement of goods and in the placement of tools such as conveyor belts and packers.
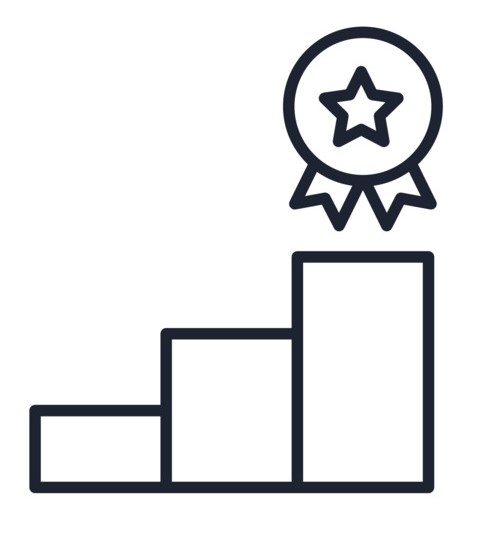
NOT PRIORITIZING INVENTORY
Sure, products are a company’s metaphorical baby, however you cannot afford to treat all inventory equally on the warehouse floor. Every product comes with their own storage, demand, and handling requirements that must be planned around.
- High demand items should be shelved in forward-picking locations, allowing your pickers quick access to them.
- Seasonal items may benefit from having a rotating inventory placement based on expected demand.
- Accurate forecasting will save you paying costly overhead for slow-moving overstock items.
- Group like inventory together for efficient location and picking.
- Regular inventory audits can help ferret out obsolete or forgotten items at the back of your warehouse.
Treating all inventory as equal is one of the most common warehousing mistakes that cost businesses. Understanding the needs of each product will help you build an inventory plan to maximize your workflow.
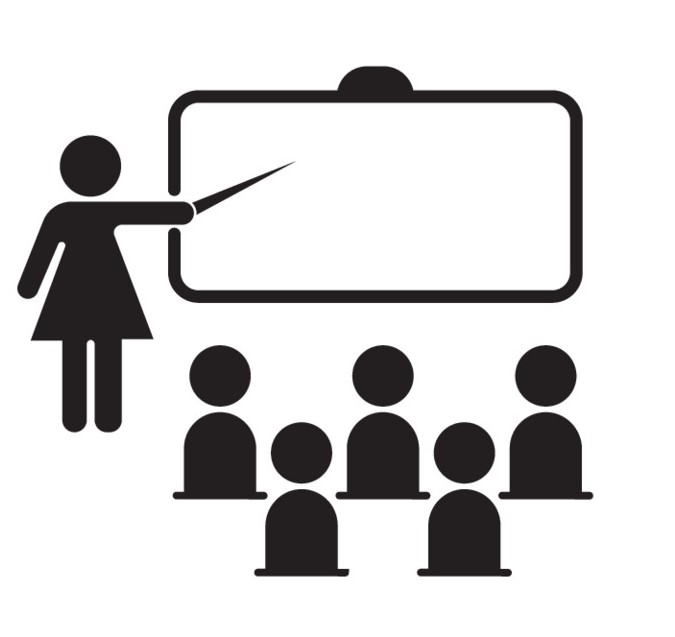
A LACK OF PROCESS
Knowing the products you have on the shelf is only half the battle. If each employee handles your inventory in a different manner, even the best planned warehouse will run into problems. When it comes to receiving, storage, picking, packing, and shipping – uniformity is the name of the game.
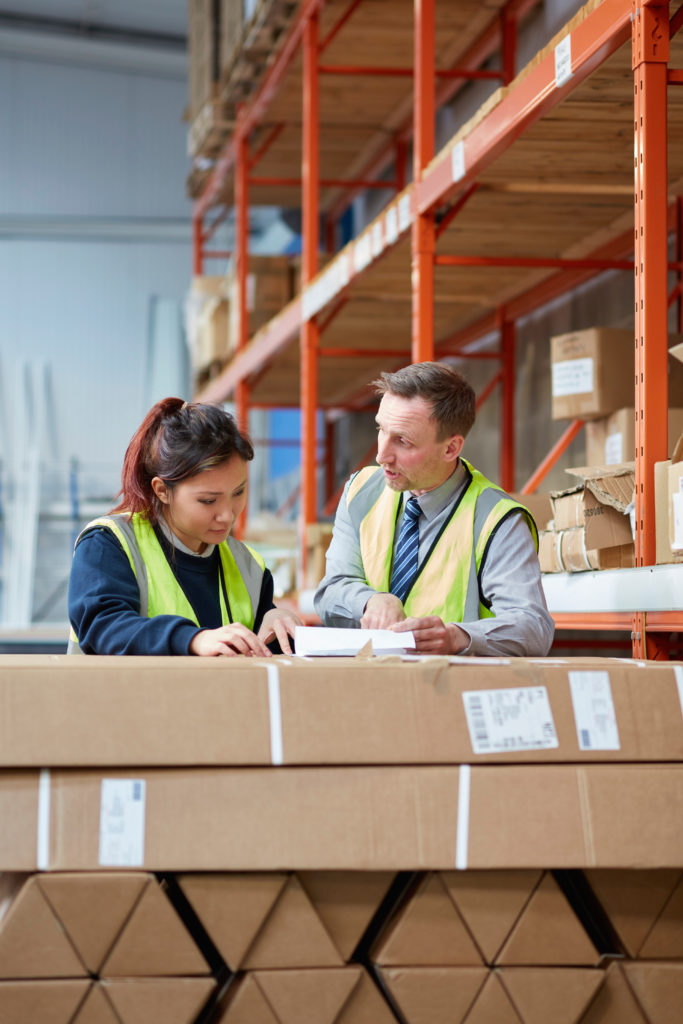
All warehouse employees need to perform tasks in the same way as their peers. This will avoid errors, quality control problems, and efficiency gaps. The first thing that happens when an employee is assigned to a new area of the warehouse should be teaching the established process. Not having protocols in place is setting your warehouse up for a number of expensive issues down the road. When creating these processes, work with your employees familiar with the task to build the best system to tackle the job. Write down the process and build a culture of mentorship as employees move between areas in your facility.
The demands and stresses on running your facility have never been greater, but eliminating these common warehousing mistakes gives your operation the competitive advantage it needs and avoids burning through your company’s capital.
Subheading graphics provided by Vecteezy