Last week we looked at how cross-docking can improve your productivity and reduce delivery lead times. But you may be asking, what is cross-docking? In its purest form, it is the process of moving inventory direct from a truck in receiving to an awaiting truck at shipping:
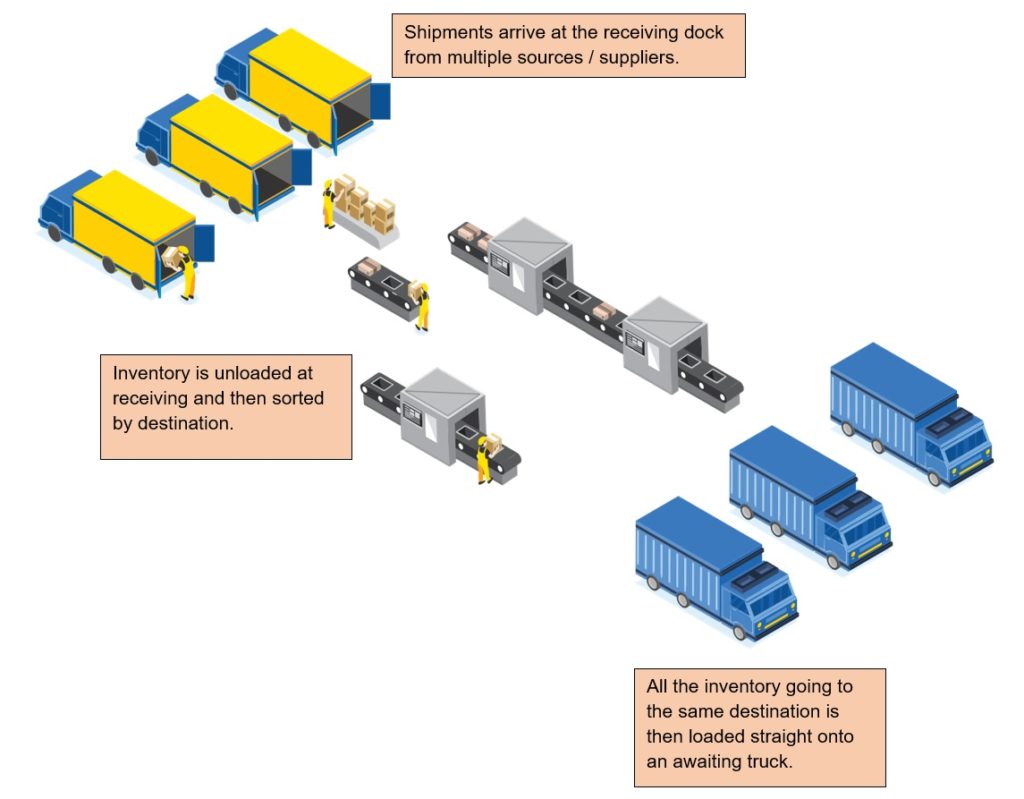
You may already practice cross-docking when you take inventory from an inbound truck to a person in the office. Maybe it is a letter or inventory sample. It is something that does not need to go into storage. If you have been in an LTL operation you have seen pure cross-docking where no inventory is stored (at least long term).
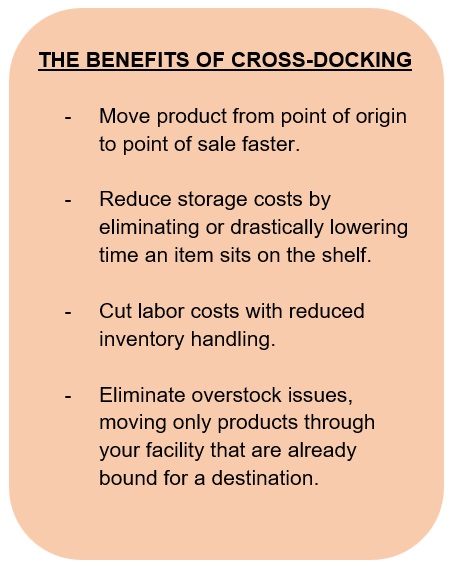
If you already have traditional pick and ship operations, you may not have the capacity or resources to try full cross-docking, but there are still options.
HYBRID CROSS-DOCKING METHOD
Rather than moving inventory direct from receiving to shipping, can you set up a small section of racks near the shipping area that can be used for storage and subsequent picking?
If yes, you could store higher active inventory in these smaller sections for easier retrieval. Because you are technically putting the inventory into storage and subsequently picking the product, it is not classified as cross-docking. But having the inventory available closer to the point of use (shipping) will allow you to realize some of the benefits of cross-docking.
But how do you know which inventory to pilot with this approach? The answer will depend on your business system capabilities. Do you have systems to help identify open orders waiting for inventory or soon to be orders not yet released? This could be a starting point. If you have visibility to the orders and associated line-item details, you could plan to stage any inventory on these line items in the smaller storage zone near shipping. But it takes planning and system support, things we will explore next week in more detail as we look at Five Ways a WMS Improves Customer Service.
ABOUT THE AUTHOR:
Chris Barnes is the Supply Chain Doctor and part of the APICS Coach network. He holds a B.S., Industrial Engineering with an Economics Minor, from Bradley University, and an MBA with emphasis on Industrial Psychology with Honors from the University of West Florida. He is one of the few people in the world to hold CPIM-F, CLTD-F and CSCP-F designations from ASCM/APICS.
GRAPHICS:
Provided by Vecteezy