In a recent post we referenced that a manager’s tools available are labor, space, and equipment. For certain operations with the correct order profiles, there is a way to improve labor productivity and reduce delivery lead times which will help reduce costs and improve customer service, and potentially save space. This is a method known as cross-docking. Let’s take a look at how it might work for you…
WAREHOUSING
Traditional warehouse operations are designed to receive inventory, put the inventory into storage and pick the inventory for shipment. This model works well for companies who have customers willing to wait a few days for delivery. This approach also helps manage and satisfy demand variability with higher days on hand inventory and safety stock. But traditional warehousing also adds cost to operations.
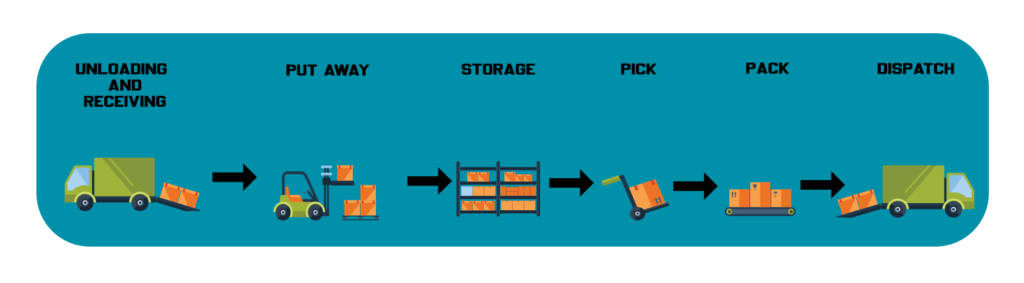
In past posts on developing a business case for warehouse management systems, we discussed the large labor cost bucket and costs of carrying inventory found in traditional operations. Adding in the growing pressures of shortened delivery lead times driven by same day or next day delivery and you start to realize warehousing needs to adapt.
There is a way.
CROSS-DOCKING
Imagine if you knew in advance, inbound inventory was now, or soon to be needed for an outbound order? Why would you put the inventory away, deep into the storage bays in the warehouse. It will take time and labor to put the inventory into storage, plus time and labor to get the inventory picked for shipment preparation. If your inventory, operations, and systems can meet a few key characteristics, you may be able to benefit from cross-docking.
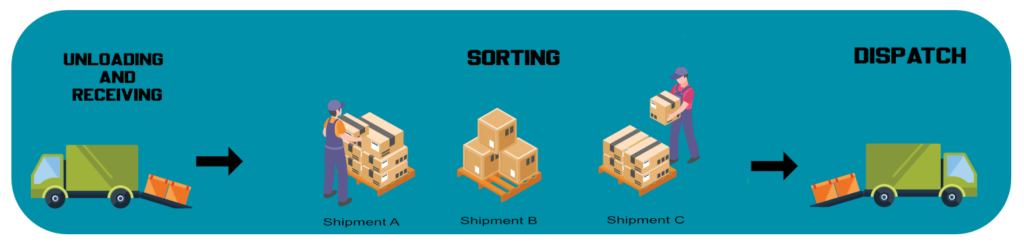
In its purest form, cross-docking is the process of moving inventory direct from a truck in receiving to an awaiting truck at shipping. There are several variations of cross-docking and certain conditions to be met for this to be implemented successfully. We will discuss some of these in our next post.
ABOUT THE AUTHOR:
Chris Barnes is the Supply Chain Doctor and part of the APICS Coach network. He holds a B.S., Industrial Engineering with an Economics Minor, from Bradley University, and an MBA with emphasis on Industrial Psychology with Honors from the University of West Florida. He is one of the few people in the world to hold CPIM-F, CLTD-F and CSCP-F designations from ASCM/APICS.GRAPHICS:
Designed By macrovector / Freepik